In einer zunehmend digitalisierten Industrie steht ein Begriff im Fokus vieler Entscheider: Predictive Maintenance (vorausschauende Instandhaltung). Während klassische Wartungsstrategien auf festen Intervallen oder dem Eintreten eines Schadens basieren, geht Predictive Maintenance einen entscheidenden Schritt weiter – sie erkennt potenzielle Ausfälle, bevor sie überhaupt entstehen. Durch den Einsatz von Sensorik, Datenanalyse und Künstlicher Intelligenz (KI) ermöglicht diese Methode nicht nur eine höhere Anlagenverfügbarkeit, sondern auch massive Kosteneinsparungen.
Doch wie funktioniert Predictive Maintenance genau? Welche Technologien stehen dahinter? Für welche Branchen lohnt sich der Einsatz besonders – und welche konkreten Vorteile lassen sich beziffern? In diesem Blogartikel beantworten wir all diese Fragen umfassend. Du erhältst einen praxisnahen Überblick über die Funktionsweise, die Vorteile und die Herausforderungen, die mit der Einführung eines PdM-Systems einhergehen – ergänzt durch aktuelle Marktdaten, reale Anwendungsbeispiele und Zukunftsperspektiven.
Was ist Predictive Maintenance?
Predictive Maintenance (auf Deutsch: vorausschauende Instandhaltung) ist eine moderne Wartungsstrategie, die auf Datenanalyse und Echtzeitüberwachung basiert. Ziel ist es, den optimalen Zeitpunkt für eine Wartung vorherzusagen, bevor ein Ausfall oder ein größerer Schaden eintritt. Im Gegensatz zu traditionellen Wartungsarten, wie der reaktiven („Reparatur nach Defekt“) oder präventiven Wartung („Wartung nach Zeitintervallen“), nutzt Predictive Maintenance fortschrittliche Technologien, um fundierte Entscheidungen zu treffen.
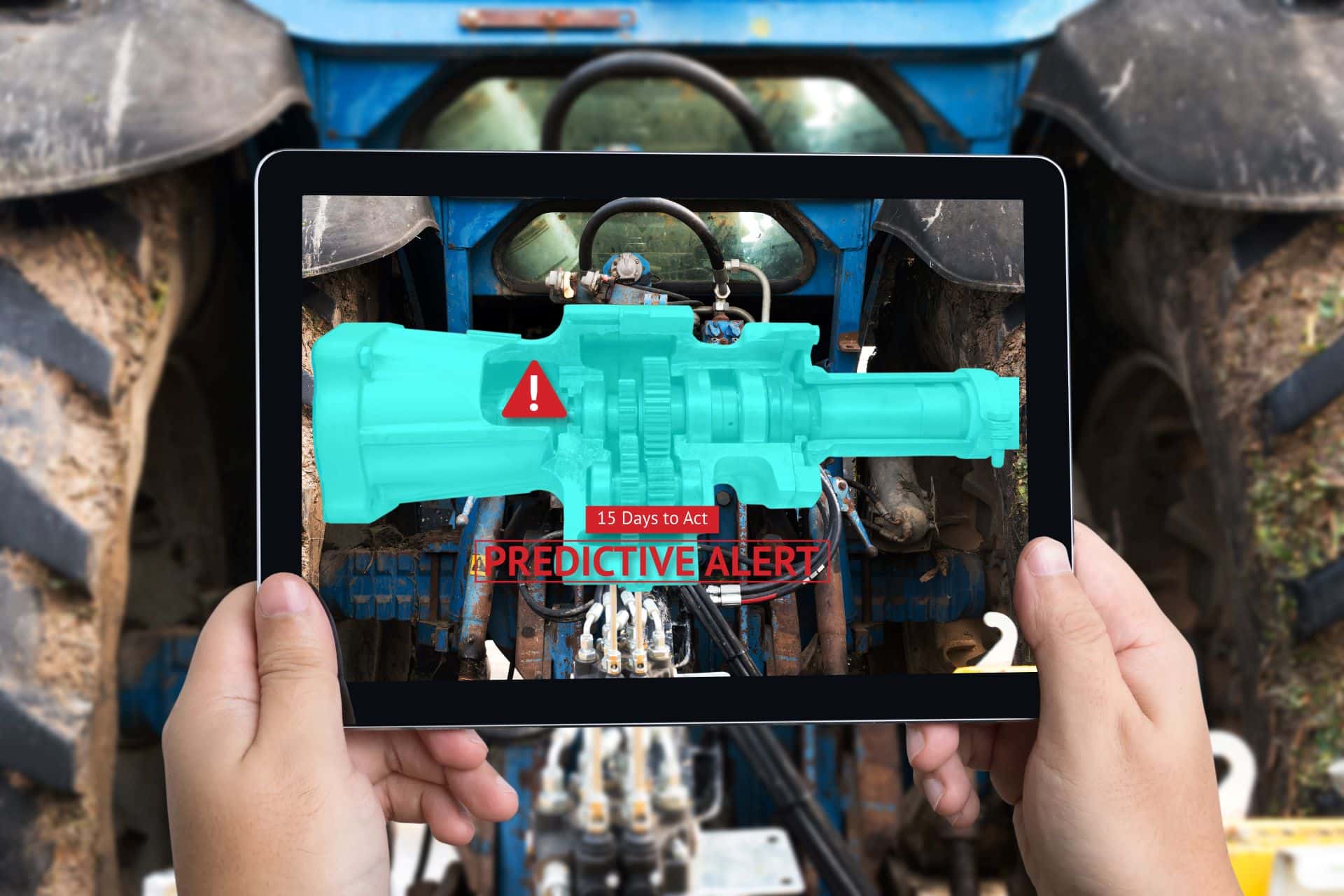
Die Grundlagen von Predictive Maintenance
Ein PdM-System besteht in der Regel aus folgenden Bausteinen:
-
Sensorik: Erfasst Daten wie Temperatur, Vibration, Stromstärke, Feuchtigkeit oder Druck direkt an der Maschine.
-
Datenanalyse: Algorithmen analysieren die gesammelten Werte auf Muster oder Abweichungen.
-
Künstliche Intelligenz / Machine Learning: KI erkennt Abnutzungserscheinungen, prognostiziert Ausfallwahrscheinlichkeiten und leitet daraus Handlungsempfehlungen ab.
-
Visualisierung & Alerts: Dashboards oder Benachrichtigungen helfen Technikern, rechtzeitig einzugreifen.
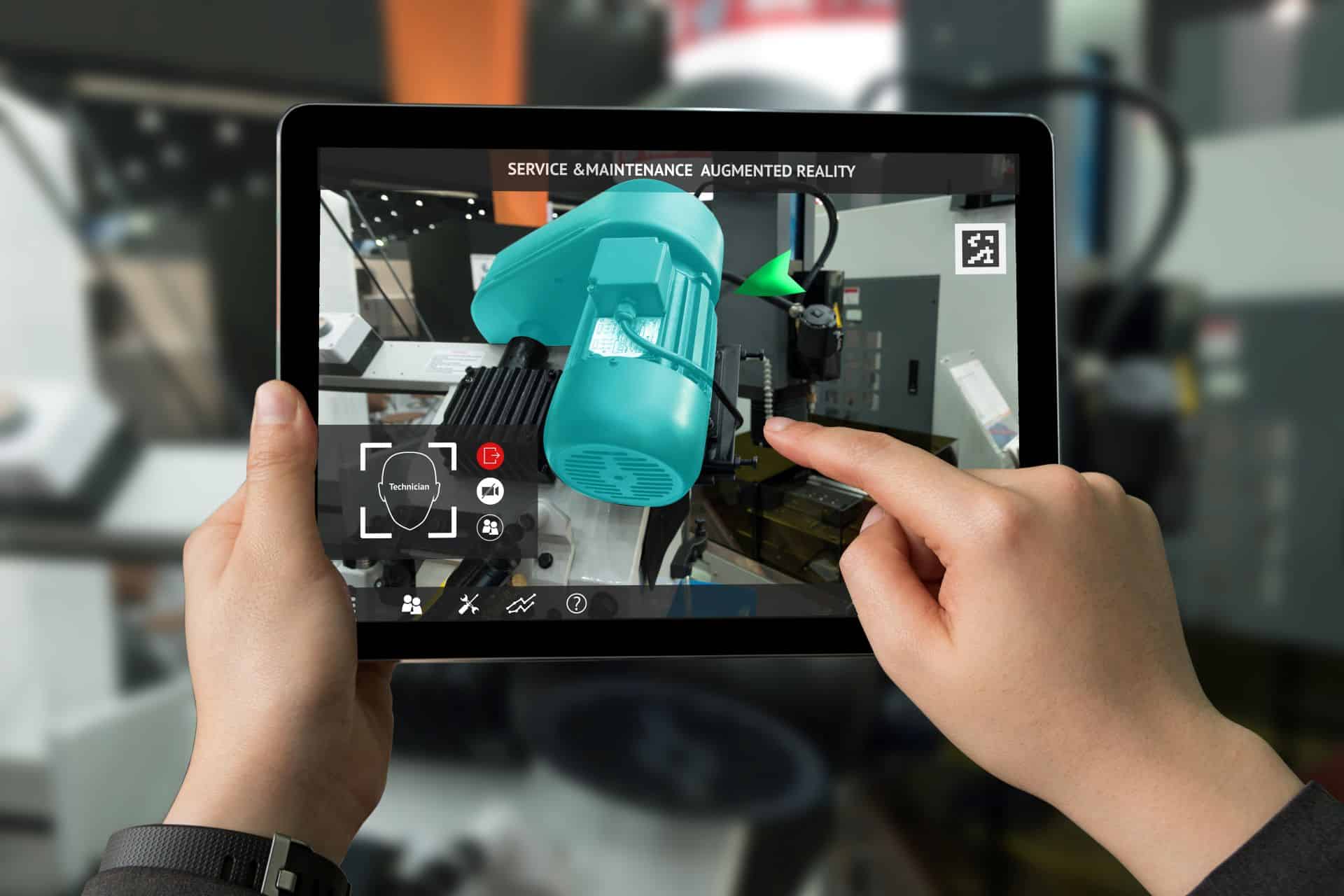
Unterschied zu anderen Instandhaltungsformen
Wartungsform | Beschreibung | Reaktion auf Probleme |
---|---|---|
Reaktiv (korrektiv) | Eingriff nach Ausfall | Keine Vorwarnung |
Präventiv (zeitbasiert) | Wartung in regelmäßigen Intervallen | Vorbeugend, aber ineffizient |
Condition-based | Wartung bei Grenzwertüberschreitung | Basiert auf Zustand, aber unpräzise |
Predictive Maintenance | Vorhersage gestützt durch Daten & Algorithmen | Proaktiv & präzise |
Mit Predictive Maintenance lassen sich ungeplante Ausfälle reduzieren, die Wartungskosten senken und gleichzeitig die Lebensdauer von Maschinen verlängern.
Welche Vorteile bietet Predictive Maintenance? – Nutzen & KPIs im Überblick
Predictive Maintenance ist kein technischer Selbstzweck, sondern bietet messbare betriebswirtschaftliche Vorteile. Unternehmen, die auf vorausschauende Instandhaltung setzen, berichten von erheblichen Effizienzgewinnen, reduzierten Kosten und höherer Anlagenverfügbarkeit.
Die wichtigsten Vorteile im Überblick
1. Reduzierte Wartungskosten
Da nur bei tatsächlichem Bedarf gewartet wird, sinkt der Aufwand für unnötige Inspektionen oder den Austausch noch funktionstüchtiger Komponenten. Laut einer Studie von PwC können so bis zu 12 % der Instandhaltungskosten eingespart werden.
2. Minimierte Ausfallzeiten
Ein geplanter Eingriff ist schneller, günstiger und risikoärmer als eine Notfallreparatur. Predictive Maintenance kann die Zahl ungeplanter Ausfälle um bis zu 70 % senken – laut Deloitte lassen sich damit Produktivitätsverluste massiv reduzieren.
3. Verlängerte Lebensdauer von Maschinen
Regelmäßige, zielgerichtete Wartung verhindert Folgeschäden und erhält die Leistung von Maschinen über längere Zeiträume. Studien berichten von einer Lebensdauerverlängerung um 20 % oder mehr.
4. Gesteigerte Betriebssicherheit
Verschleißteile, elektrische Fehler oder mechanische Probleme können frühzeitig erkannt und behoben werden – bevor sie ein Sicherheitsrisiko darstellen.
5. Positiver ROI
Laut McKinsey liegt der durchschnittliche Return on Investment (ROI) von PdM-Projekten zwischen 10 % und 30 % – und über 90 % der Unternehmen berichten von einem finanziellen Nutzen innerhalb der ersten 12 bis 24 Monate nach Implementierung.
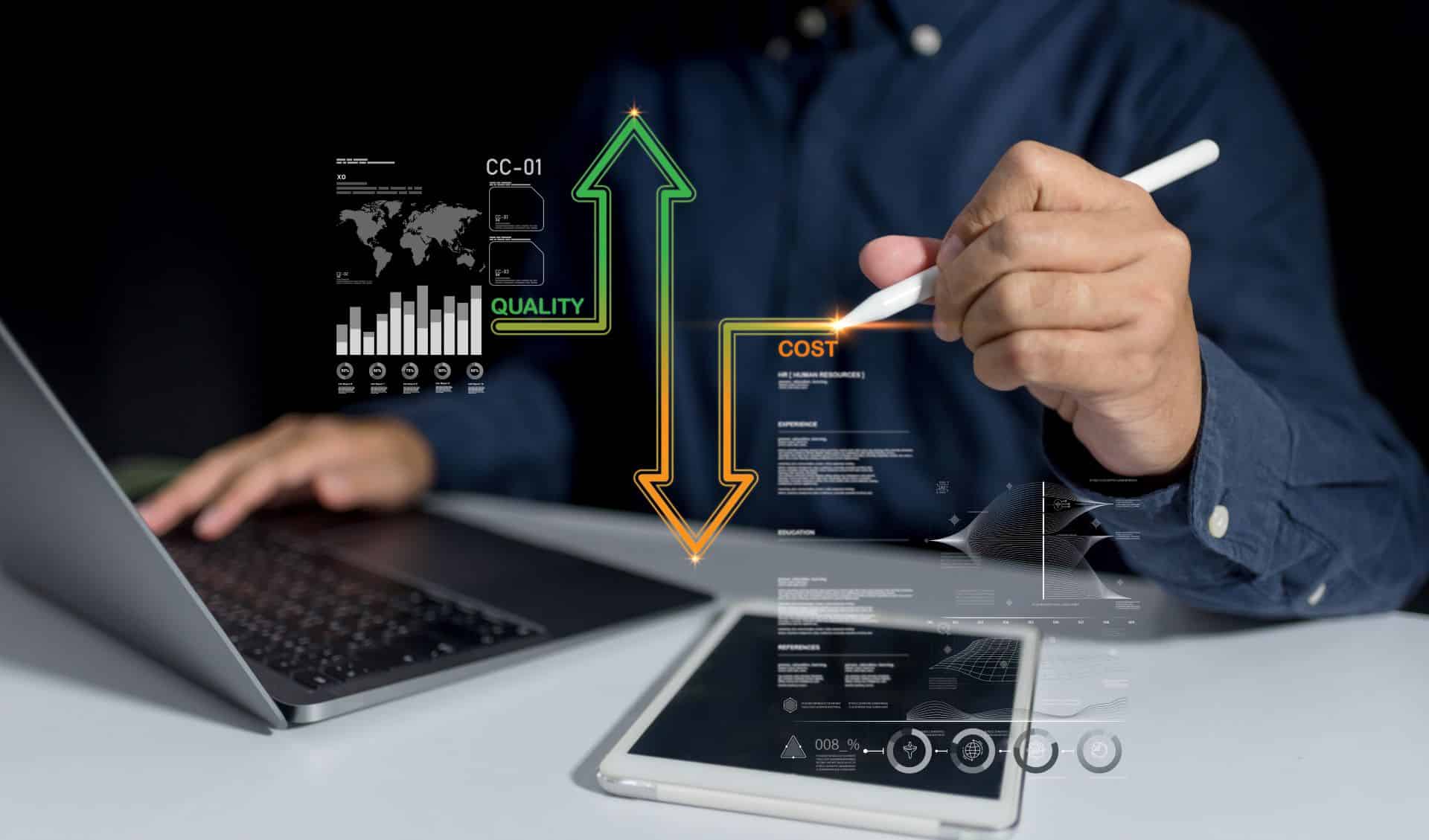
Konkrete Kennzahlen aus der Praxis
Kennzahl | Durchschnittswert | Quelle |
---|---|---|
Reduktion der Wartungskosten | bis zu 25 % | Deloitte, PwC |
Senkung ungeplanter Ausfälle | 30–70 % | McKinsey, GE Digital |
Verfügbarkeit von Anlagen | Steigerung um bis zu 9 % | PwC |
Lebensdauer der Maschinen | Verlängerung um 20–40 % | Siemens, IBM |
ROI | > 95 % positive Rückmeldungen | GE, Infosys, Accenture |
Amortisationsdauer | 6 bis 18 Monate | World Economic Forum |
Marktentwicklung & Zukunftstrends: Predictive Maintenance als Wachstumsmotor
Der Markt für Predictive Maintenance wächst rasant – angetrieben durch steigende Anforderungen an Effizienz, Nachhaltigkeit und digitale Transformation in der Industrie. Unternehmen weltweit investieren gezielt in Predictive-Maintenance-Lösungen, um Wettbewerbsvorteile zu sichern.
Marktvolumen & Prognosen
Laut verschiedenen Marktanalysen zeigt sich ein klarer Aufwärtstrend:
Jahr | Marktvolumen | Wachstumsrate (CAGR) |
---|---|---|
2022 | 5,5 Mrd. USD | – |
2025 (Prognose) | ca. 10 Mrd. USD | ca. 20 % p. a. |
2030 (Prognose) | > 25 Mrd. USD | bis zu +26 % CAGR |
Besonders in der Fertigungsindustrie, im Transportwesen, der Energiebranche und in der Luftfahrt steigt die Nachfrage rasant. Die Verbreitung von IoT-Geräten, Edge Computing, sowie der Siegeszug von Künstlicher Intelligenz und Cloud-Lösungen machen Predictive Maintenance für viele Unternehmen erstmals wirtschaftlich umsetzbar.
Technische Funktionsweise: Wie Predictive Maintenance in der Praxis arbeitet
Ein erfolgreiches PdM-System vereint verschiedene Technologien und Prozesse zu einem intelligenten, lernenden Überwachungssystem.
1. Sensorik & Datenerfassung
Zuerst werden an den Maschinen Sensoren installiert, die kontinuierlich Werte wie:
-
Temperatur
-
Vibration
-
Schall
-
Stromverbrauch
-
Feuchtigkeit
-
Druck
messen. Diese Daten werden über IoT-Geräte in Echtzeit gesammelt und an eine zentrale Datenplattform gesendet.
2. Datenintegration & Vorverarbeitung
Die Rohdaten müssen bereinigt, standardisiert und gespeichert werden – häufig in der Cloud oder auf lokalen Edge-Geräten. Anschließend folgt eine Vorverarbeitung: Normalisierung, Feature-Engineering, Datenfilterung.
3. Datenanalyse & KI-Modelle
Hier setzt die „Magie“ ein:
Algorithmen analysieren Muster und erkennen Anomalien, Verschleißsignale oder Fehlverhalten. Häufig eingesetzte Methoden sind:
-
Klassifikationsmodelle (z. B. Random Forest, XGBoost)
-
Anomalie-Erkennung (z. B. Isolation Forest, PCA)
-
Zeitreihenanalyse (z. B. ARIMA, LSTM)
-
Remaining Useful Life (RUL)-Schätzung
Mit Machine Learning verbessert sich die Genauigkeit dieser Vorhersagen laufend.
4. Alerts, Dashboards & Maßnahmen
Wird ein Risiko erkannt, werden Techniker über Dashboards, Apps oder E-Mails informiert. Die Systeme bieten oft konkrete Handlungsempfehlungen – z. B. Austausch eines Bauteils in 12 Tagen oder Reduzierung der Maschinenlast.
5. Rückkopplung & Lernen
Moderne Systeme sind lernfähig: Sie vergleichen Vorhersagen mit tatsächlichen Ereignissen und optimieren ihre Modelle kontinuierlich. Explainable AI (XAI) gewinnt dabei an Bedeutung – sie erklärt, warum eine bestimmte Warnung ausgelöst wurde.
Konkrete Anwendungsfälle von Predictive Maintenance: Maschinen im Fokus
Predictive Maintenance funktioniert nicht nur im großen Stil, sondern kann gezielt für spezifische Maschinentypen eingesetzt werden. Je nach Bauart und Funktion kommen unterschiedliche Sensoren und Analysemodelle zum Einsatz. Hier sind die häufigsten und wirkungsvollsten Maschinen-bezogenen Use Cases im Überblick:
🌀 1. Pumpen
Typische Probleme: Leckagen, Kavitation, verstopfte Leitungen, Lagerschäden
Erfasste Messwerte:
-
Vibration (z. B. bei Unwucht oder Wellenversatz)
-
Druckabfall oder -spitzen
-
Temperaturveränderungen am Gehäuse
-
Durchflussrate
Was PdM bringt: Frühzeitige Erkennung von Verschleiß und Unregelmäßigkeiten erhöht die Lebensdauer und senkt Reparaturkosten. Besonders wichtig in Wasserwerken, Chemieanlagen oder Lebensmittelverarbeitung.
⚙️ 2. Elektromotoren
Typische Probleme: Überhitzung, Lagerausfall, Wicklungsschäden
Sensorik & Datenpunkte:
-
Stromaufnahme (Anomalien in der Phase)
-
Lager-Vibration
-
Isolationswiderstand
-
Temperatur des Gehäuses oder der Wicklungen
Wirkung: PdM reduziert das Risiko eines plötzlichen Stillstands, z. B. in Produktionslinien oder Fördersystemen. Einen systematischen Überblick über geeignete Messpunkte und Verfahren für unterschiedliche Maschinenarten bietet diese praxisorientierte Zusammenstellung von typischen Predictive-Maintenance-Anwendungsfällen.
📦 3. Förderanlagen & Lagertechnik
Typische Probleme: Riemenverschleiß, Blockaden, Rollenversagen
Relevante Datenquellen:
-
Motorlast und -strom
-
Geräuschanalyse (z. B. bei Rollen)
-
Temperatur von Lagern
-
Geschwindigkeit und Laufzeiten
Nutzen: Besonders in der Logistikbranche unverzichtbar. Vorausschauende Wartung verhindert Stillstand in hochautomatisierten Verteilzentren (z. B. Paketverarbeitung oder Palettenlager).
🛠 4. Werkzeugmaschinen
Typische Probleme: Spindelverschleiß, Unwucht, Kühlmittelprobleme
Mögliche Überwachungspunkte:
-
Spindeldrehzahl und -vibration
-
Schneidkraftanalyse
-
Kühlmitteldruck und -temperatur
-
Werkzeugverschleiß über Laufzeitmodelle
Vorteil: PdM verbessert die Bearbeitungsqualität, verlängert Werkzeugstandzeiten und verhindert Ausschuss – besonders relevant in CNC-Fertigung, Formenbau oder Fräszentren.
🔧 5. Hydrauliksysteme
Hauptprobleme: Leckagen, Druckverlust, Überhitzung
Sensorik-Einsatz:
-
Ölanalyse (Partikel, Viskosität, Feuchtigkeit)
-
Druckverlaufsmessung
-
Temperaturfühler im Fluidkreislauf
Ergebnis: Vermeidung von Totalausfällen durch schleichende Systemschäden. Ideal für mobile Maschinen, Pressen oder Industriehydraulik.
Diese Use Cases zeigen, wie vielseitig Predictive Maintenance in der Praxis einsetzbar ist – und wie eine gezielte Auswahl von Sensorik und Algorithmen je nach Maschinentyp den größtmöglichen wirtschaftlichen Nutzen entfalten kann.
Anwendungsbereiche: Wo Predictive Maintenance besonders viel bewirkt
Predictive Maintenance ist längst nicht mehr auf Großkonzerne beschränkt – zahlreiche Branchen profitieren inzwischen von dieser Technologie.
1. Fertigungsindustrie
Hier zählt jede Minute: Ein Maschinenstillstand kann mehrere hunderttausend Euro kosten. Predictive Maintenance erkennt z. B. Lagerprobleme, Schmierstoffmängel oder Temperaturschwankungen frühzeitig – und sichert so kontinuierliche Produktionsprozesse.
2. Transport & Bahn
Sensoren an Schienen, Weichen, Rädern oder Bremsanlagen ermöglichen eine vorausschauende Wartung und erhöhen Sicherheit und Verfügbarkeit – z. B. bei der Deutschen Bahn oder SNCF.
3. Luftfahrt
Predictive Maintenance reduziert nicht nur Wartungskosten, sondern verhindert Flugverspätungen. Systeme überwachen Triebwerke, Hydraulik oder Klimaanlagen. Airbus setzt z. B. auf „Skywise“ – eine PdM-Plattform mit KI-Analyse in Echtzeit.
4. Energie & Öl/Gas
Ob Windkraftanlage, Pipeline oder Bohrinsel – Predictive Maintenance hilft, kritische Ausfälle in sensiblen Umgebungen zu vermeiden und erhöht die Versorgungssicherheit.
5. Logistik & Lagerhaltung
In automatisierten Lagern (z. B. Amazon, DHL) sichern PdM-Lösungen den reibungslosen Betrieb von Förderbändern, Robotern und Verpackungsmaschinen.
Herausforderungen & Grenzen: Was bei Predictive Maintenance beachtet werden muss
So vielversprechend Predictive Maintenance ist, sie bringt auch Hürden mit sich – besonders bei der Einführung.
1. Hohe Anfangsinvestitionen
Sensoren, IoT-Systeme, Softwareplattformen und Datenteams kosten Geld. Der ROI ist zwar oft gut, doch der Break-even-Point liegt meist erst nach 6–18 Monaten.
2. Datenqualität & -verfügbarkeit
PdM braucht große Mengen valider Daten. Viele Unternehmen kämpfen mit fragmentierten Datensilos, inkompatibler Hardware oder fehlender Historie.
3. Komplexe Modellierung
Jede Maschine ist anders. Algorithmen müssen individuell trainiert und angepasst werden. Zudem sind Fehlalarme oder falsch-negative Prognosen besonders kritisch.
4. IT-Sicherheit
Vernetzte Anlagen bedeuten auch neue Angriffsflächen. Predictive Maintenance muss in ein robustes Sicherheitskonzept eingebettet werden – inklusive Zugriffsschutz, Monitoring und Patches.
5. Change Management
Technologie ist nur ein Teil. Mitarbeiter müssen geschult, Prozesse angepasst und Verantwortlichkeiten geklärt werden. PdM funktioniert nur, wenn Technik, Mensch und Organisation zusammenspielen.
Implementierung in der Praxis: So führst du Predictive Maintenance erfolgreich ein
Der Weg zu einem funktionierenden Predictive-Maintenance-System ist kein Sprint, sondern ein strukturierter Prozess. Unternehmen sollten schrittweise vorgehen:
Schritt 1: Zieldefinition & KPIs festlegen
Welche Maschinen sind kritisch? Welches Ziel verfolgst du – Kostenreduktion, höhere Verfügbarkeit oder Sicherheitsgewinn? Definiere messbare KPIs wie „Mean Time Between Failures (MTBF)“, „Downtime“ oder ROI.
Schritt 2: Pilotprojekt starten
Beginne mit einem kleinen Anwendungsbereich (z. B. 1–2 Anlagen), um Technologie und Prozesse zu testen. Nutze Edge-Geräte oder bestehende Sensorik, um erste Daten zu sammeln.
Schritt 3: Daten erfassen & analysieren
Übertrage Maschinendaten sicher in ein zentrales System. Starte mit einfachen Auswertungen (z. B. Schwellenwertanalysen) und entwickle mit der Zeit komplexere KI-Modelle.
Schritt 4: Modelltraining & Validierung
Trainiere deine Algorithmen mit historischen Daten. Arbeite mit Data Scientists oder spezialisierten Anbietern zusammen. Nutze KPIs wie „Precision“ und „Recall“, um Prognosequalität zu messen.
Schritt 5: Integration & Rollout
Sobald die Ergebnisse zuverlässig sind, erfolgt die Integration ins operative Geschäft – inkl. Dashboards, Alarmmanagement und Prozesse für Wartungsteams.
Schritt 6: Skalierung & Optimierung
Stelle auf weitere Anlagen oder Standorte um. Verbessere Modelle kontinuierlich durch Feedbackschleifen („continuous learning“). Automatisiere mehr Entscheidungsprozesse.
Ausblick: Die Zukunft der Instandhaltung ist intelligent
Predictive Maintenance ist erst der Anfang. Immer mehr Unternehmen entwickeln sich weiter in Richtung „Intelligent Maintenance“ – ein Zustand, in dem Systeme selbst lernen, Entscheidungen treffen und sich autonom optimieren.
Kommende Trends:
-
Explainable AI (XAI): KI-Ergebnisse werden transparenter, um Vertrauen zu schaffen.
-
LLMs & Chatbots: Wartungstechniker können Systeme per Spracheingabe befragen („Was ist der wahrscheinliche Fehler bei Maschine A?“).
-
Maintenance-as-a-Service (MaaS): Externe Anbieter übernehmen PdM vollständig – auf Abo-Basis.
-
Autonome Wartungssysteme: Roboter, Drohnen und mobile Apps für Inspektion und Reparatur.
-
Integration mit ESG-Zielen: Nachhaltigkeitskennzahlen werden mit Wartungsdaten verknüpft (z. B. Energieverbrauch, CO₂-Ausstoß pro Ausfall).
Fazit: Vorausschauend statt stillstehend
Predictive Maintenance ist kein Hype – sondern eine Schlüsseltechnologie für die Wettbewerbsfähigkeit moderner Industrieunternehmen. Sie senkt Kosten, steigert Verfügbarkeit und verbessert die Planungssicherheit.
Wer frühzeitig in Sensorik, Datenkompetenz und intelligente Algorithmen investiert, schafft die Grundlage für langfristigen Erfolg – und macht Instandhaltung vom Kostenfaktor zum Wettbewerbsvorteil.
Bildnachweis:
Gorodenkoff – stock.adobe.com
zapp2photo – stock.adobe.com
Kornkanok – stock.adobe.com